4.2 UNSCHEDULED MAINTENANCE
4.2.1 Discrepancy Management System
- Discrepancy Tracking System:
- A Discrepancy Tracking System (DTS) will be utilized to record every discrepancy, technical failure, or non-conformity of the FSTD flagged by regulatory authorities, users, or employees and a controlled Excel File will be used to record discrepancies. The discrepancy tracking system shall consist of following details,
- Unique Discrepancy Record number
- Discrepancy Status
- Categorisation / Prioritisation
- Description of the Problem
- Date Raised along with identity of the Reporter
- MMI categorisation
- Estimated Correction Period
- Details of action taken and the identity of the person with date of action
- Downtime details
- System Category
- Logistics
- OEM & TDM support details
- Date of closure and snag clearance record
- Identity of the person closing
- Impact on Training
- Any other details (As required, TM discretion)
- Any discrepancy reported by the user or technician that cannot be replicated either by the Engineering staff or the user, may be resolved immediately by making an appropriate note in the log sheet, need not to be recorded as a discrepancy unless it falls as per below point c.
- Any downtime claimed by the FSTD user must be accompanied with the Discrepancy Record (DR) even if the root cause is cleared within end of session, so that any discrepancy interrupting the training shall have a record.
- Any discrepancy logged by the user shall be informed to the following subsequent crew by evidently showing the recorded comments in previous user log.
- Discrepancy List (DL):
- DL is a list, containing all "Open" and "On offer" training discrepancies affecting any kind of training, evaluation, or a check.
- If any Discrepancy listed is identified as "MMI", it shall contain a "DGCA MMI" tag along with its "IMPACT OF TRAINING" as declared by Head of Training.
- Each FSTD's respective DLs (Discrepancy List) shall be generated if any changes are made to the current DL and prominently published adjacent to the FSTD. This list should be reviewed and updated as per MMI policy Para 4.2.2 as required.
- Discrepancy Review: All open discrepancies are required to be assessed by both the technical staff and management, in accordance with section 4.2.6 - Progression Check on Corrective Maintenance.
- Manufacturer Support: Anydiscrepancy requiring assistance from the TDM will be directed to respective Customer Support. In addition to the discrepancies recorded in the DTS, the technical staff may raise additional queries with the TDM as needed.
4.2.1.a MISSING, MALFUNCTIONING OR INOPERATIVE (MMI)
[GUIDANCE BULLETIN- GB/14/2021/FSTD]
MMI component refers to any equipment or parts that are absent, damaged, or not functioning properly, and can adversely affect the satisfactory completion of a training Manoeuvre, Procedure, or Task. This can include physical components such as machinery, electronic devices, or structural elements, as well as software or other intangible components.
Responsibilities:
- Engineering Personnel:
- Shall inform the HoT on Training discrepancy reported by the user or identified in house during maintenance.
- May also assist in any discrepancies requiring a technical overview and engineering judgement.
- May assist in reviewing the discrepancy impact on FSTD's performance or handling qualities, for those involving out-of-tolerance QTG validation tests as specified in OC 15 of 2014.
- Updating the Discrepancy List published for the user.
- Providing detailed corrective actions taken to close the MMI discrepancies and any component replacement carried out for the closure.
- Quality Manager:
- Shall monitor the MMI status and report any MMI discrepancies to authority when exceeding 30 days.
- QM shall be the primary Point of Contact to DGCA.
- QM shall submit the List of all training discrepancies categorised as MMI to DGCA FOI (concerned with FSTDs) on quarterly basis via email.
- MMI list shall contain the corrective actions, evidence ofpart procurement (if logistics involved) outto close the MMI discrepancies and an explanation from Head of Training stating why the snag is not affecting Pilot Training and mitigation plan if any.
- The sample of MMI reporting form to DGCA shall be as specified in attachment - 08 of OC 15/2014 Issue - II.
- Head of Training:
- Shall review the discrepancy for MMI categorisation, discrepancy prioritisation and publish the Impact of Training.
- Declaring the discrepancy MMI categorisation and DR prioritisation is discreet to Head of Training.
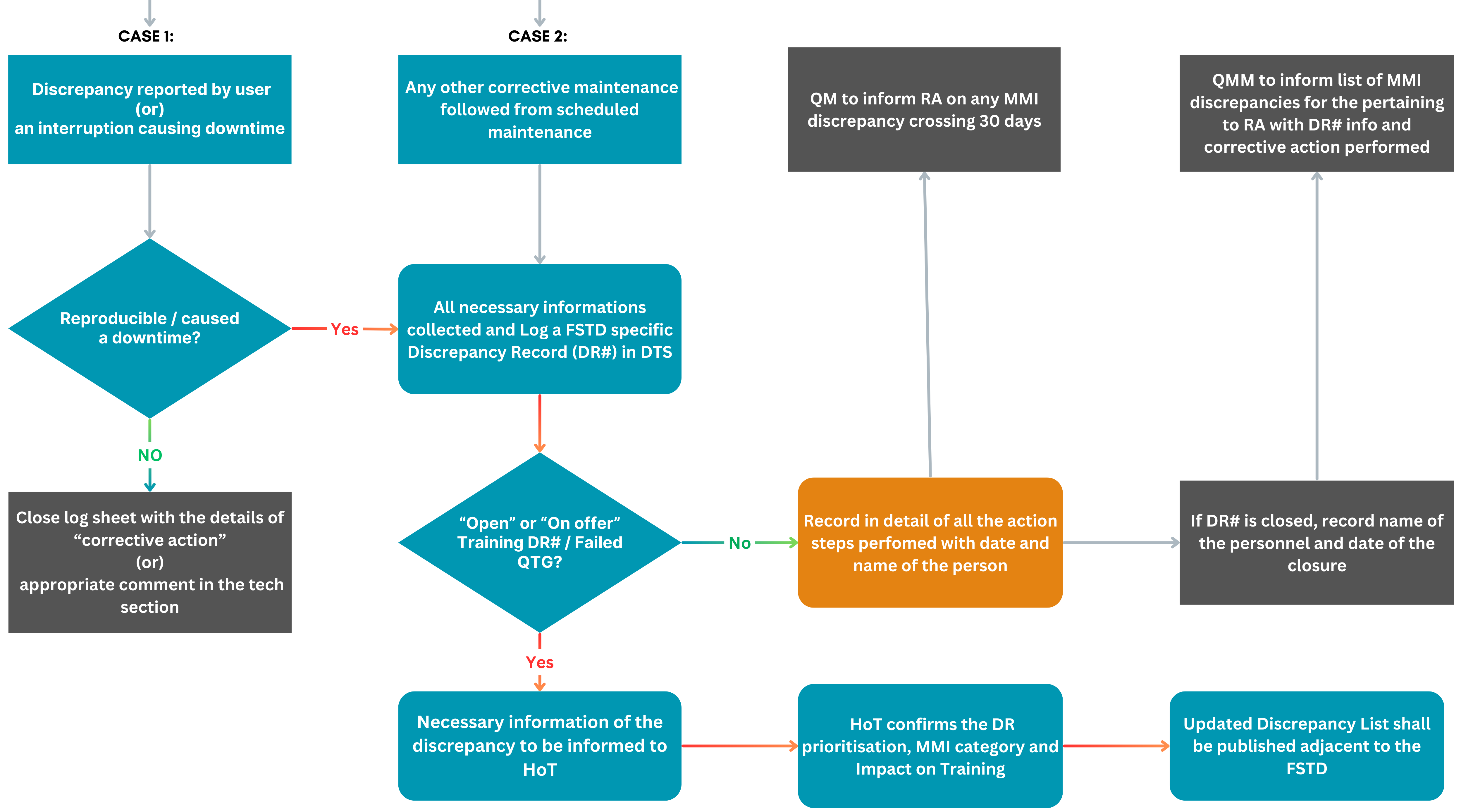
4.2.1.b MMI GUIDELINES
In determining if a particular FSTD discrepancy is an MMI component reportable to the NSP in accordance with OC 15/2024 Issue-2 Attachment - 8, the following guidelines from DGCA STD Guidance Bulletin -14 as prescribed may be used if required,
- Does the discrepancy affect or require a change to the FSTD Statement of Qualification (SOQ)?
- Does the discrepancy affect the performance or handling qualities of the FSTD?
- This condition includes the reporting of out-of-tolerance Qualification Test Guide (QTG) validation tests conducted to meet FSTD evaluation requirements of CAR 7/D/VI paragraph 28.1.a.
- Does the discrepancy affect the accomplishment of tasks (as defined in Appendix A, Table A1B, Appendix B, Table B1B, Appendix C, Table C1B or Appendix D, Table D1B of OC 15/2014 as applicable) for training, checking, or testing in the FSTD in accordance with the DGCA approved training program(s) being conducted in the FSTD? FSTD discrepancies falling in point 4 & 5 are not considered as MMI:
- Airport visual model database discrepancies that do not completely prevent the use of an airport model listed on the FSTD Statement of Qualification (SOQ).
- Minor FSTD versus aircraft configuration item differences that do not adversely affect training, testing, checking tasks.
4.2.2 ACAT MMI POLICY
- ACAT FSTD Discrepancy Tracking System will be updated by ACAT Engineering to reflect MMIs (Missing, Malfunctioning, or Inoperative) as soon as it is identified.
- Before any training session, information on all open Training discrepancies including MMIs will be readily available to the instructor. It is the discretion of the instructor to determine the type of training restriction imposed due to the MMI, and to decide whether it is viable and safe to accept the Simulator with the MMI for the planned training session. This is applicable for both DRY & WET training.
- Additionally, as a proactive measure to facilitate planning of FFS training, as soon as a discrepancy is identified and updated on the discrepancy tracking system, ACAT Engineering will intimate the Head of Training with the details of discrepancy.
- As much as feasible, the Head of Training will publish the Impact on Training, MMI categorisation and DR priority which shall be updated in the discrepancy list and published near the FFS. Any change to the status of an existing MMI and details of additional MMIs, if any, will also be updated as prescribed by HoT.
- Each MMI component installed and required to operate correctly to meet the current Statement of Qualification, must be repaired or replaced within 30 calendar days, unless otherwise required or authorized by the DGCA. ACAT Quality will notify DGCA as required.
- The QM must submit the MMI list for all FSTDs to the DGCA Headquarters quarterly, including corrective actions, closing dates, procurement evidence, and an explanation from the HOT as to why the snag is not affecting Pilot Training. This list shall be submitted via email to CFOI and the relevant Dy. CFOI/FOI.
4.2.3 DISCREPANCY PRIORITIZATION SYSTEM (DPS)
The Priority Assignments Guideline is provided to ensure standard reporting of discrepancy status within the ACAT. The goal is to prioritise the discrepancies depending upon their impact on FSTD performance and restriction it has and close within the target resolution period listed.
The Estimated Completion Date (ECD) of each discrepancy must be updated on a regular basis by the technical staff. The ECD must be logical.
- Training Discrepancy: A discrepancy that requires corrective action and impacts the training of crews or affects qualification of the device.
- Target Resolution Timeframe: A target period established by Technical Staff to meet client expectations.
- Maximum Allowable Correction Period [MACP]: A period in which a Training discrepancy is targeted to correct so the important issue will be focused on priority. In case of an MMI & AOG to meet competent authority's requirements and other certain category of discrepancy must be reported as per section 4.2.7 of this Manual.
- Maintenance Discrepancy: A discrepancy that requires corrective action but does not impact any user functionality of experience, training, or check.
Training Discrepancy
Priority | Description | MACP |
---|---|---|
AOG | Aircraft (FSTD) on Ground, no training, testing, or checking possible and / or safety hazard. | 7 Days |
A | Restricts training, testing, or checking, and/or prevents the agency evaluation, and/or affects FSTD qualification level, and/or is a potential safety hazard or MMI issue applicable to DGCA (No Workaround) | 30 days |
B | Restricts training, testing, or checking or prevents specific training, testing, or checking. (Workaround Possible) | 120 days |
C | Detracts from optimum operation of FSTD. Minimal effect on training, testing, or checking or qualification level of FSTD, other than MMI items | 180 days |
Maintenance Discrepancy
Priority | Description | MACP |
---|---|---|
A | Restricts training, testing, or checking, and/or prevents the agency evaluation, and/or affects FSTD qualification level, and/or is a potential safety hazard or MMI issue applicable to DGCA (No Workaround Possible) | 30 days |
B | Restricts training, testing, or checking or prevents specific training, testing, or checking. (Workaround Possible) | 120 days |
C | Detracts from optimum operation of FSTD. Minimal effect on training, testing, or checking or qualification level of FSTD, other than MMI items | 180 days |
4.2.4 Aircraft on Ground (AOG)
When an FSTD has been confirmed to be on AOG, it is implied that FSTD is unserviceable for more than 30 minutes continuously during a scheduled session. If confirmed an AOG the following must be done by an engineering personnel:
- Immediately inform scheduling and Technical Manager or delegate asap
- Send an e-mail to "ACAT AOG Group" with the subject line "(SIM Pneumonic) - AOG NOTIFICATION" and the e-mail must include the following details,
- Simulator Affected
- Customer Name
- Reported Time
- Reason for the AOG
- Any other relevant information
- Scheduling shall take updates from engineering personnel as required, till STD is recovered from AOG.
- If AOG Support is required from TDM, contact TDM Customer Support, providing all details which have been troubleshooted so far.
- Call the AOG support Hotline and provide reference of the Snag and email.
- Send an Email to AOG Support of the Manufacturer with all possible and relevant Details if needed.
Once the AOG has been resolved, the following must be done:
- Immediately, inform scheduling and TM or delegate as soon as possible.
- Send an e-mail to "ACAT AOG Group" with the same subject line. The e-mail must include the following details,
- Simulator Affected
- Customer Name
- Root Cause
- Resolved Time
- Device Failure Time
- Lost Training Time
- Any other relevant information
4.2.5 AOG PART REQUIREMENT
- If an AOG is caused due to unavailability of spare and immediate procurement is needed, technical manager or delegate should evaluate the severity, gathering as much as information on the spare and initiate the procurement asap.
- Necessary departments and members of ACAT are alerted on the requirement to expedite the process.
- Necessary documents shall be recorded for the procurement on the purchase if AOG need to be reported to any regulatory body as described in section 4.2.7 of this manual.
4.2.6 PROGRESSION CHECK
All Open discrepancies of each FSTD shall be reviewed periodically in various levels as below,
- Weekly (Engineering staff)
- Transfer / Copy the discrepancies to the TDM customer support if required.
- Review on the action taken and prioritisation to close MACP.
- Any components or spare used for corrective maintenance.
- Engineering staff and Technical Manager / delegate may discuss the discrepancy for any additional attention needed.
- Monthly
- TM or delegate shall evaluate the overall technical performance of each FSTD.
- All open MMI items may be discussed with HoT or delegate if any assistance needed.
- Quarterly
- The AM, TM, QM, and HoT or their delegates shall review all long open training Discrepancies of each simulator and discuss in detail.
- If the discrepancies are open or unattended too long, appropriate action should be planed as required, record of the discussion shall be maintained.
-
Note: The reviews on the DR's crossing the MACP shall be recorded
in DTS with valid reason and plan of action, transfer of discrepancy to TDM support
if needed.
4.2.7 DISCREPANCY REPORTING GUIDELINES
If the discrepancy affects qualification level or the safe use of the training device the users and the authority must be informed by QM/CMM on the nature of the discrepancy and its estimated repair time. This also applies for MMI components. In the below conditions, as per the Table the concerned Authorities shall be informed via CMM/QM
S.no | Discrepancy | EASA | DGCA |
---|---|---|---|
1 | For a training AOG discrepancy exceeding its "Maximum Allowable Correction Period" | YES | YES |
2 | The discrepancy creating an unsafe condition if the FSTD is used for training. | YES | YES |
3 | The discrepancy is a Maintenance discrepancy. | NO | NO |
4 | The discrepancy is a MMI (Missing, Malfunctioning, or Inoperative) component and the "Maximum Allowable Correction Period" has been exceeded. | NO | YES |